News
How to Measure Warehouse Efficiency
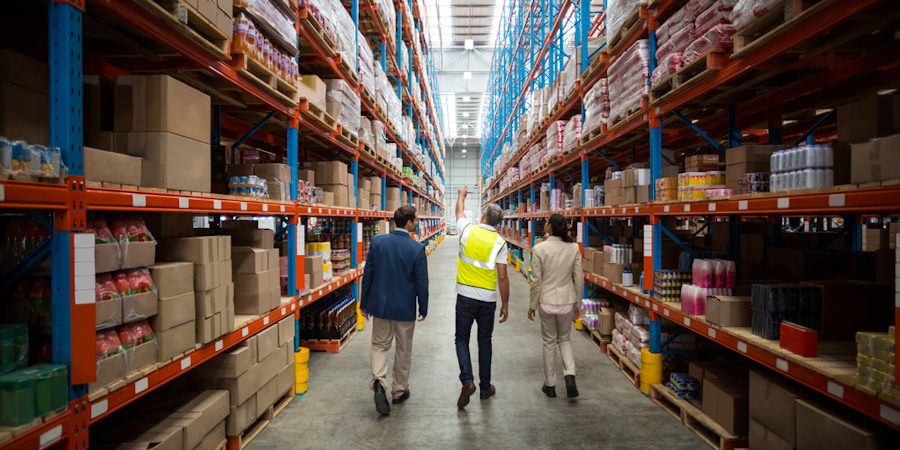
Benefits of Measuring Warehouse Efficiency
The major benefit for warehouse management is that the data acts as the most solid foundation to plan changes to warehouse layout, loading, or shipping dock changes, and staff reduction.
Reviewing your warehouse efficiency data allows you to make informed decisions on a wide range of business vectors from stock management, to staff training and forklift truck maintenance. Measuring warehouse efficiency also allows your stakeholders to get a realistic picture of your operation, giving them the peace of mind they seek.
Staying mindful of actual stock errors, vendor issues, and upcoming events will help balance the struggles that pickers face when trying to fill orders.
By looking at how customers are experiencing your services, you can break down the common problems that are being reported. Further disassembling productivity and labour into accuracy and speed metrics helps identify problems during the fulfilment process.
How to Measure Warehouse Efficiency
Operational Efficiencies
Your forklift truck fleet and warehouse staff are best measured by the number of activities performed in a given period. The volume of incoming and outgoing shipments can be monitored and compared to previous periods to evaluate gains and losses in performance. Other measures of operational efficiency include labour hours as a percentage of weekly sales and forklift truck maintenance downtime.
Warehouse Stock and Storage
Items are ideally placed by location, height and handling to aid operational efficiency. Monitoring inventory for items with high turnover rates helps you further optimise your placement and streamline productivity by reducing congestion. Shelf vacancy rates can also be assessed, ensuring that hard-to-reach locations have higher vacancies, or are stocked with low-turnover items.
What to Measure
Pick Speed
Items picked per day or week. Measure this metric against the number of staff employed during that period to know the average output per staff member.
Fill Rate
The number of items that are being picked against the number of items being ordered.
Order accuracy
The number of items that are being correctly scanned into and out of bin locations.
Downtime
The amount of time between items being picked, usually due to distance between bin locations.
Stock Levels
Items that are on back order from the manufacturer, causing orders to get backed up.
Seasonal trends
Tracking trends according to the seasonal changes allows you to plan ahead.
Fulfilment Performance
Fulfilment is about giving the customer what they want, when they expect it. If your warehouse goes from 50 to 75 orders shipped daily (a 50% increase), you still need to maintain levels of speed, accuracy, safety and care when dealing with the additional 25 orders. Direct measures such as on-time orders, order accuracy and shipping damage can be gleaned from customer complaints and feedback. New customers and customer retention compared between time periods can illustrate customer satisfaction with both product and fulfilment of orders.Inventory Accuracy
Sales, order and inventory management software allows for precise tracking of your inventory. But sales alone do not account for shrinkage, count errors, breakages or other discrepancies. Measuring actual inventory conditions against sales records provides a check for inventory databases, preventing over and under-stocks. Monitoring turnover cycles and comparing these to sales cycles provides optimal levels of stock, so that a warehouse is stocking exactly the correct amount of each item.Measuring efficiency helps identify problems both long standing and newly arising. Once you start tracking your efficiency data, you can monitor your long term performance and plan for the future, while checking for sudden data fluctuations that often indicate a performance issue.Subscribe
Keep up to date with PHL and all things forklift machinery.